One of the most important and time consuming aspects to processing timber is getting it dry – and it can be more challenging than you might think.
To be classified as ‘dry’ (or ‘seasoned’), the moisture content of the wood needs to be below 20%, with 10% an ideal figure for interior and exterior use.
For context, freshly-cut wood has a moisture content typically starting around 40% – and even potentially as high as 200%!
The reason wood can have a moisture content of over 100% is because it’s calculated by comparing the weight of the water with the dry weight of the wood (weight of water / dry weight of wood × 100) – it’s not a percentage of the freshly-cut weight.
Why is it important that wood is dry?
Compared to wet (or ‘green’) wood, dry wood is more durable, stable, workable and combustible. This makes it superior for all applications, from fine furnituremaking to burning as wood fuels.
- Durability – moisture is the best friend of wood-decaying fungi and microorganisms. Wet wood is more susceptible to rot, insect infestations and weakening over time. A lower moisture level makes it much harder for these threats to thrive.
- Dimensional stability – wood is hygroscopic – when it absorbs moisture, it expands and when it dries out, it shrinks. This process can lead to warping and cracking. If wet wood is not dried in a controlled way, it can shrink unequally and cause damage.
- Workability – wet wood can cause blades to gum up and clog up sanding equipment. Not only this, but it’s also slippery and more difficult to handle. Dry wood is easier to machine, allows for cleaner cuts and holds fixings more readily.
- Easier to finish – woodcare finishes do not adhere optimally to moist surfaces. Because dry wood has open pores, it is more receptive to uptake of treatments, stains and oils. They penetrate more deeply, giving a longer-lasting and higher-quality finish.
- Burns cleaner – when wet wood is burned, it kicks up a lot more smoke. The water vapour released from the wet wood dampens the fire, making the whole combustion process less efficient. This leads to creosotes build up, less heat and more pollutants – all things that dry wood minimises.
So, how are these low levels of moisture actually achieved?
Wood drying process explained
Once the tree has been felled and the wood has been debarked, sawn into ‘cants’, edged, trimmed and roughly graded, drying can begin. The first step for this is called ‘sticking’. Then, the wood can either be air dried or kilned.
In this video, Joe, our Managing Director, walks you through the steps involved.
Sticking
The prepared wood boards will be placed on a base so it is elevated from the ground, preventing moisture absorption.
Then, small spacers (called ‘stickers’) will be placed in between every layer of wood in the pack. This allows air to flow freely between the layers throughout the drying process. This is also known as ‘sticking’ or ‘stickering’.
A roof or tarp may be used to protect the stack from rain but still allow for air circulation.
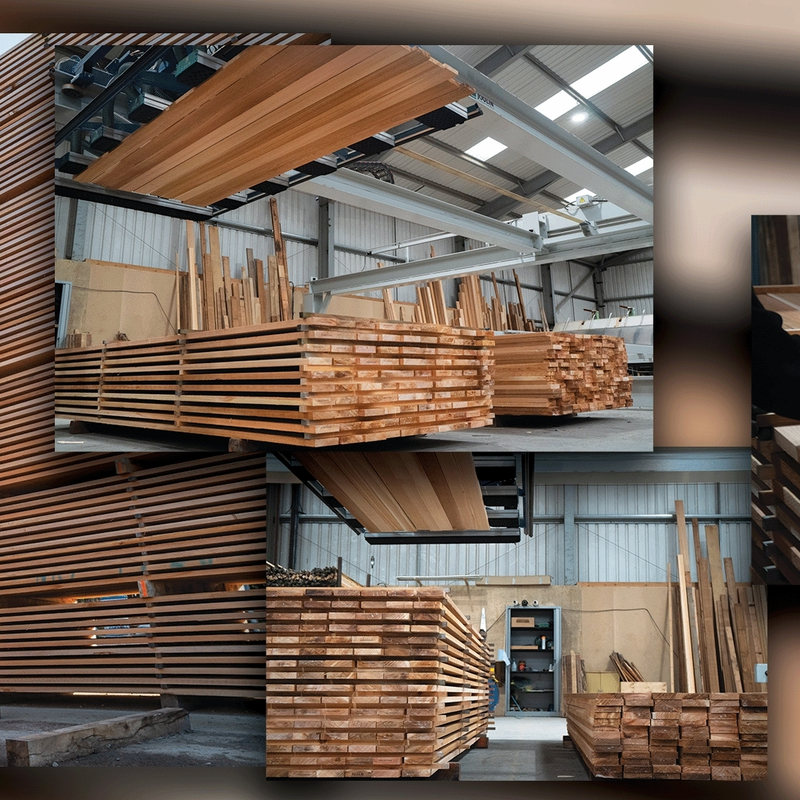
Air drying
The wood can be left to naturally air dry in a sheltered, breezy location. This simply involves relying on outdoor heat and air circulation to reduce the moisture content of the timber.
This is quite a long process, however. It is dependent on local temperature, humidity and wind levels. To reach a moisture content of around 15%, it can take around one year per inch of wood thickness in a temperate climate.
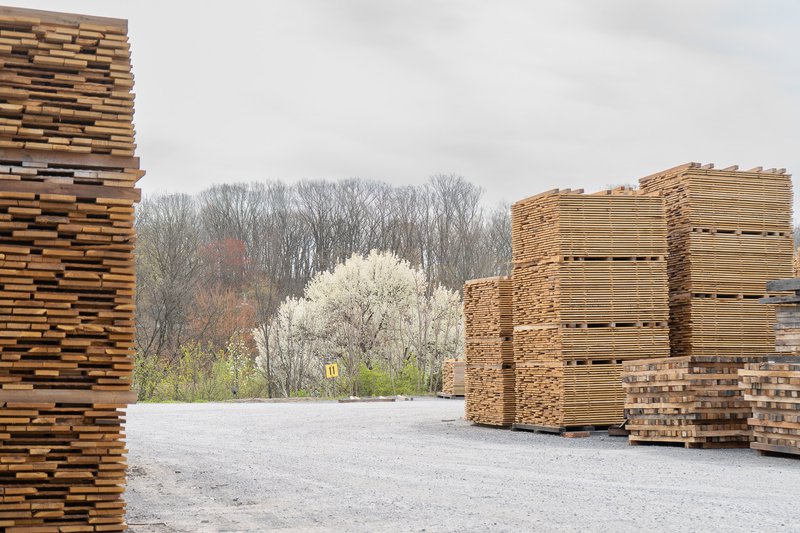
Kilning
Kiln drying is a faster, more controlled alternative to air drying. It takes place in a large enclosed chamber and involves blowing hot air on the sticked packs of wood – essentially, a purpose-built oven for wood.
Two popular types include:
- conventional kilns: the most common industrial kiln, suited to large-scale operations. Hot air is generated by a boiler, often powered by waste sawdust. In the control room, temperature, relative humidity (using vents) and air flow (using fans) are all regulated to give precise environmental control.
- dehumidification kilns: an electric-powered closed-loop system, popular for smaller-scale operations. After drying the wood, moist, warm air comes in contact with refrigeration coils. This condenses the moisture into a liquid which is drained as cool water. The cool, dry air is then reheated using a heat pump and reused.
Temperatures used in the kiln are dependent on the species, but usually start around 40°C and are slowly raised to around 60°C.
The moisture content of the wood is monitored using probes and physical samples. The wood may be conditioned towards the end of its drying process – this involves using humidification to relieve any internal stresses and prevent the outer layers drying too fast.
The kiln drying process can take mere days, but is usually at least several weeks. Once the timber is dried to an appropriate moisture content – around 8% for indoor use and fine woodworking – it is then taken out of stick. Then, the wood can be properly graded and sorted.

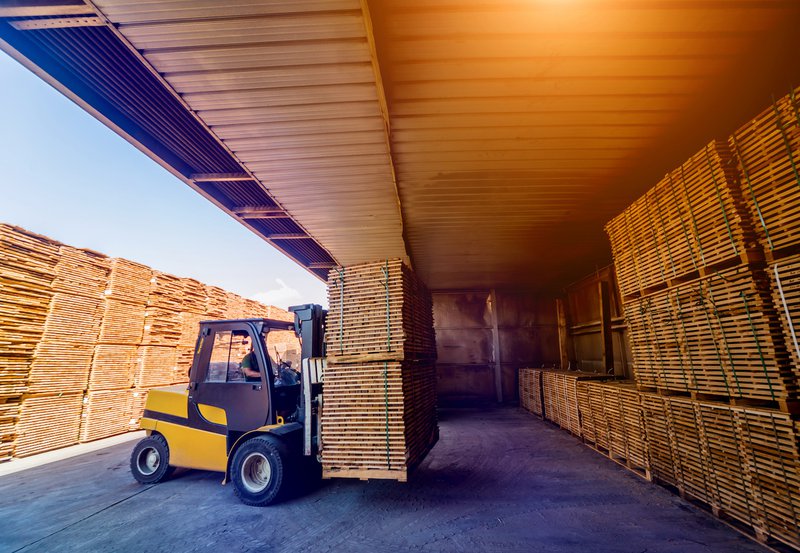
For smaller-scale in hotter climates, solar kilns use a greenhouse-style mechanism with fans circulating the air. Vacuum kilns are another specialist type of kiln – the vacuum allows moisture to evaporate at a lower temperature, which is helpful for shorter drying times for smaller volumes of wood.
Pre-drying
Sticked wood packs can be pre-dried before being kiln-dried. This takes place in an enclosed building with enormous fans that blow air between the sticked packs of wood.
These fans will change the direction they blow in to ensure an even distribution across the wood. This is similar to a kiln, except without the hot air and precise environmental controls. Pre-drying helps to remove a large portion of the green wood’s moisture before it enters the kiln.
As well as reducing energy consumption in the kiln, by safely reducing moisture in a controlled way, pre-drying helps to avoid drying defects like honeycombing – this is where cracks form a honeycomb-like pattern on the wood’s interior.
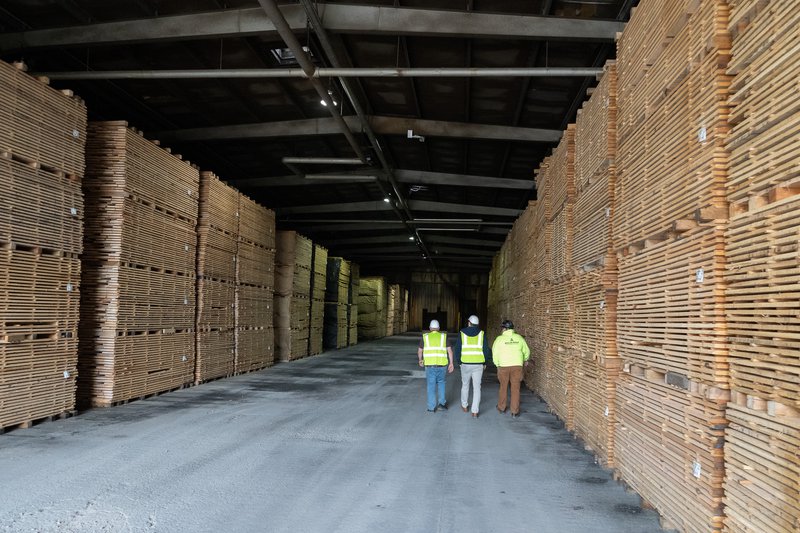
Post-drying storage
The air- or kiln-dried wood should then be stored in a dry, ventilated, covered area, avoiding contact with the ground. These conditions should stay as consistent as possible – remember, as wood is hygroscopic, it can reabsorb moisture.
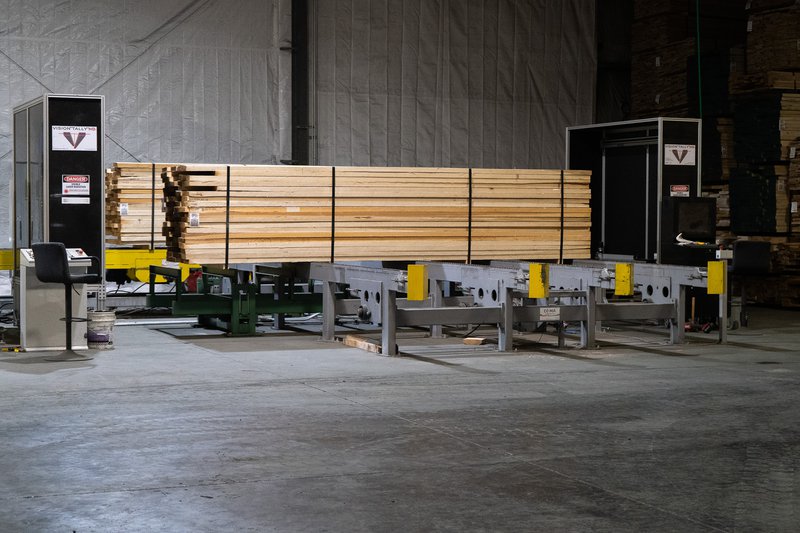
Does dried wood go back to its old moisture level?
Once it’s been air- or kiln-dried, the wood will come into equilibrium with the moisture level of the air surrounding it – a point known as the ‘equilibrium moisture content’.
In a particularly humid outdoor environment, this means the wood’s moisture content may increase to around 12–18%. However, unless it’s placed in soaking conditions, it won’t go back to the moisture content percentage of green wood (>40%).
The key is to keep the wood in a controlled environment, or consider using a sealant to slow down moisture exchange. You may also want to cover up any outdoor wood with a waterproof tarp.
Duffield Timber: excellence from forest to finish
Enjoyed this read? We’ve actually written in a little more detail about the entire journey wood goes on during its manufacture.
Check out our Instagram feed too for a glimpse into timber manufacturing processes – we’ve posted plenty of behind-the-scenes footage from our trips to visit suppliers across North America.
We are a leading UK supplier of high-quality timber and machined timber products, including sawn timber, cladding, decking, fencing, oak beams, oak structures and wood fuels.
If you’re nearby, pop in to see us – we’re just off the A1 near Ripon, North Yorkshire!
Get in touch with our team