We've just completed a fantastic trip through the United States and Canada, going behind the scenes at several timber sawmills. Here's a rundown of what we saw!
As a leading timber importer in the UK, our objective was to connect with suppliers, explore new partnerships, and get a close look at the latest technology used in the industry. If you follow us on Instagram or Facebook, you may have already seen some of our updates.
The timing of our trip was opportune, coinciding with recent changes in tariffs on timber imports. This provided us with an excellent opportunity to discuss future supply plans and pricing strategies with our suppliers, ensuring we are well-prepared for what may come.
Our journey across North America: from Tennessee to Montreal
Beginning in Tennessee, we visited an oak supplier specialising in high-quality, slow-grown oak from the slopes of the Appalachian Mountains.
Next, we travelled north into prime Tulipwood (poplar) territory, starting with a visit to a longstanding supplier with operations in Virginia and New Hampshire. These regions are renowned for quality Tulipwood (poplar), particularly Virginia. Its temperate climate, abundant rainfall and fertile soil are ideal conditions for the steady growth of high-quality timber.
Continuing from the northeast coast of America, our journey took us through Vermont and across the border into Canada. Here, our focus shifted to maple, black walnut, and ash.
The majority of our white hard maple is sourced from Quebec, Canada, due to the timber's exceptional quality and colour. The cold climate, consistent rainfall, and winter harvesting all contribute to the desired lighter colour.
We also had the opportunity to see how black walnut is processed. This included how it is steamed – this draws moisture through the timber to even out the colour and achieve the desired aesthetic.
After a brief stop in Montreal, we crossed over the St Lawrence river back into the US and onwards into New York state and Pennsylvania. Travelling through these states, we visited a further six sawmills, taking in cutting-edge sawmill technology.
The latest sawmilling technology: de-barking, sawing, sorting, drying
For the final stop on our trip, we continued south through Pennsylvania to visit what might not have been the largest of operations, but possibly the most impressive, featuring everything in terms of automation from log to completed pack.
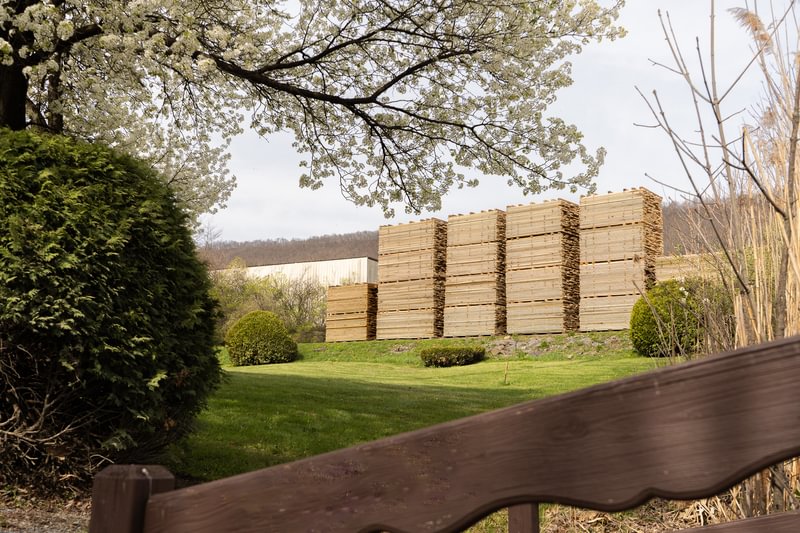
In the sawmill, the bark is stripped using a ring de-barker, followed by a single head rig saw equipped with a double-sided bandsaw blade for enhanced efficiency.
Once sawn by the operator controlled head rig saw, the waney-edged boards were sent to an edging line, while the cants (the central pieces of logs) were directed to a resaw. The resaw featured a return carousel that turned cants lengthwise before cutting them again.
Notably, boards from both the edger and resaw could be fed directly into the sorting line – a highly efficient and flexible setup.
We observed green timber (freshly-cut wood that hasn't undergone any drying or seasoning process) enter the sorting line and pass through an AI grader and trimming machine. Then, it was ink-printed with a bin number and fed into an automated bin system – which separates the boards by grade.
From here, once each bin reaches its quota, the bins are automatically lowered to a conveyor below and moved along a line to be sticked, ready for drying. Once sticked, the packs continue on the line and into an automated dipping tank for treatment, before finally being prepared for the drying process.
The drying process starts with the pre-drier, and at this facility it was a standout feature, capable of holding over one million board feet. Pre-drying takes around 30 to 40 days for 4/4” material before packs are moved to one of the site’s nineteen kilns.
After kiln drying, packs underwent a final grade check on the dry line. Boards were trimmed if necessary, removed from sticks, banded, and tallied using an automatic banding system and vision tally.
This site specialises in white oak, so we took the opportunity to review some 8/4” prime white oak. As you can see below, this timber was high-quality, with minimal defects.
In addition to nurturing these existing relationships and witnessing the latest technology the industry has to offer, we explored exciting new opportunities with a supplier of American live-edge boards.
We're delighted to report that the appropriate logistics have been arranged and the boards are now in transit, destined for Blighty!
Travelling through New York state, we also stopped by at James L Taylor Manufacturing, producers of high-quality ripping systems. With an eye to improving the efficiency and yield of production in our factory, we had a close look at a cutting-edge ripping line – including infeed and outfeed – and you can see Joe Duffield getting to grips with the workings of the line below.
Overall, the trip was a tremendous success! It reinforced our key partnerships, opened doors to new ventures, and ensured we remain up to date and adaptable in the ever-changing global trade landscape.
If you have any further questions for our team, don't hesitate to get in touch.